Процесс итеративного уточнения Пресс-форма для литья триггерного насоса включает внесение корректировок в конструкцию пресс-формы и параметры впрыска для постепенного повышения точности и качества отливаемых деталей. Вот как это обычно работает:
1. Первоначальный проект пресс-формы. Процесс начинается с первоначального проектирования литьевой формы, которая основана на 3D-модели узла триггерного насоса. Разработчик пресс-формы создает полость и стержень, устанавливает допуски и определяет качество поверхности на основе имеющихся данных.
2. Первое испытание формования: форма изготавливается на основе первоначального проекта и проводится первое испытание формования. Это включает в себя впрыскивание расплавленного пластика в форму для изготовления образцов деталей.
3. Проверка качества. Образцы деталей проверяются на точность, качество и соответствие геометрии оригинального триггерного насоса. В ходе проверки выявляются любые несоответствия, дефекты или области, требующие улучшений.
4. Сбор данных. Данные, собранные во время проверки качества, документируются, включая измерения основных размеров и обнаружение любых дефектов. Эти данные служат основой для принятия обоснованных решений по доработке пресс-формы.
5. Корректировка конструкции пресс-формы. Разработчик пресс-формы и инженеры анализируют данные проверки и определяют, где необходимы корректировки конструкции пресс-формы. Это может включать в себя изменение полости и сердцевины, изменение допусков или изменение обработки поверхности для лучшего соответствия желаемой геометрии.
6. Восстановление компонентов пресс-формы. В зависимости от конструктивных изменений может потребоваться восстановление определенных компонентов пресс-формы, таких как полость или стержень, с учетом обновленных спецификаций. Для обеспечения точности используется высокоточная механическая обработка.
7. Второе испытание на формование. Пресс-форму собирают заново с модифицированными компонентами и проводят второе испытание на формование. Целью данного испытания является оценка влияния корректировок конструкции на качество и точность деталей.
8. Повторная проверка. Образцы деталей второго испытания подвергаются еще одному раунду проверки. Данные проверки сравниваются с данными первоначального испытания, чтобы оценить эффективность корректировок.
9. Точная настройка параметров. Помимо корректировки конструкции пресс-формы, для достижения лучших результатов можно точно настроить параметры процесса литья под давлением, такие как давление впрыска, температура и время охлаждения.
10. Повторение и постоянное совершенствование. Шаги с 6 по 9 повторяются по мере необходимости до тех пор, пока не будет достигнут требуемый уровень точности и качества. Процесс является итеративным, и каждый цикл основывается на знаниях, полученных в ходе предыдущих испытаний.
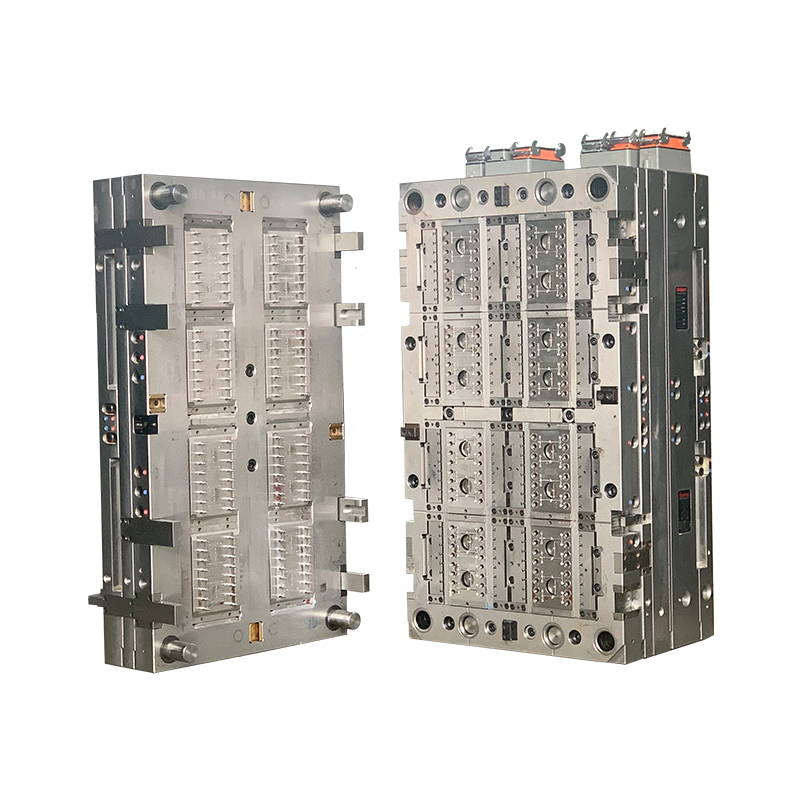
11. Окончательное тестирование и проверка. После того, как конструкция пресс-формы и параметры впрыска стабильно производят высококачественные детали, соответствующие желаемой геометрии триггерного насоса, проводятся окончательные испытания и проверка, чтобы подтвердить, что форма готова к производству.
12. Документация и ведение учета. На протяжении итеративного процесса доработки ведется документация, в которой фиксируются все изменения, внесенные в форму, и результаты каждого испытания. Эта документация служит справочной информацией для будущего обслуживания и настройки.
Итеративная доработка гарантирует, что литьевая форма триггерного насоса оптимизирована для производства деталей, которые соответствуют или превосходят требуемые стандарты точности и качества. Процесс продолжается до тех пор, пока из пресс-формы не будут последовательно получаться детали, точно повторяющие сложную геометрию узла триггерного насоса.